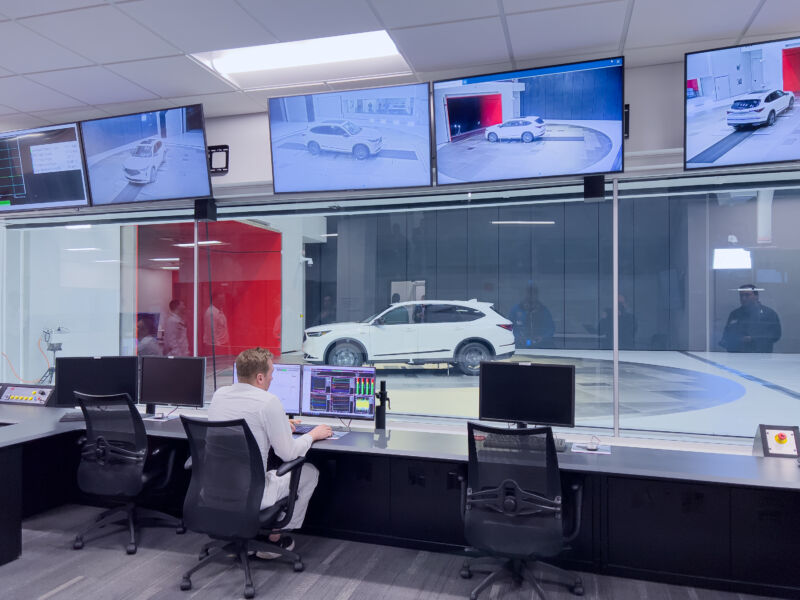
Jonathan Gitlin
EAST LIBERTY, OHIO—Over the weekend, Formula 1 burst back into action with its first race of the year. For several decades now the sport has been dominated by downforce and the application of aerodynamics. So you might think that the world’s most advanced rolling road wind tunnel would be found in England, where most of the teams are based—or perhaps in Italy’s Maranello.
But despite the sport’s well-funded emphasis on air flow, F1 is no longer the last word in rolling road wind tunnels. Now that honor belongs to Honda Automotive Laboratories of Ohio (“HALO”), where a new $124 million, 192 mph (310 km/h) facility is about to commence operations.
HALO is based at the Transportation Research Center, a vehicle proving grounds and test track a little less than an hour outside of Columbus. It’s a relatively unassuming facility from the outside, certainly compared to Ferrari’s dramatic-looking, Renzo Piano-designed tunnel in Italy. But as with people, it’s what’s inside that really matters.
-
This is the eight-meter fan that makes the wind blow.
Jonathan Gitlin -
The back side of the fan chamber
Jonathan Gitlin -
Mike Unger (left) stands in front of a set of turning vanes inside the HALO wind tunnel
Jonathan Gitlin -
An architectural drawing showing the plan view of the HALO wind tunnel. The compression nozzle and the round turntable that the rolling road fits into are visible along the lower part of the circuit.
Jonathan Gitlin
The heart—or perhaps more accurately the lung—of the eighth-mile (201.2 m) three-quarter open jet tunnel is a 26.2-foot (8 m) fan, driven by a 6,700 hp (5 MW) General Electric motor. The fan’s 12 carbon fiber blades are fixed in position, with just 0.2 inches (4 mm) of clearance to the tunnel wall. And in spite of hitting a top speed of only 250 rpm, the fan is even more well-balanced than the rotor of a turbocharger.
If 250 revolutions per minute sounds pretty low to you, you’re right—at maximum speed, the air leaving the fan is only traveling at 25 mph (40 km/h). From there the air passes through a massive 3,789 square foot (352 square meter) heat exchanger, which allows the facility to keep the air at a constant temperature, anywhere between 50-122˚ F (10-50˚ C).
“The reason why we do that is mainly for acoustic purposes. Cars are made of aluminum and plastic and carbon fiber and rubber, and they all expand and contract at different rates. So all of those things open up gaps, close gaps,” explained Honda’s Mike Unger, who’s in charge of all wind tunnel activities at HALO.
From the heat exchanger, the air travels through series of turning vanes as it makes its way around the tunnel. But the tunnel contracts through a nozzle ahead of the test room, and this compresses the air by a factor of up to 7:1, accelerating it to a maximum speed of 192 mph (310 km/h).
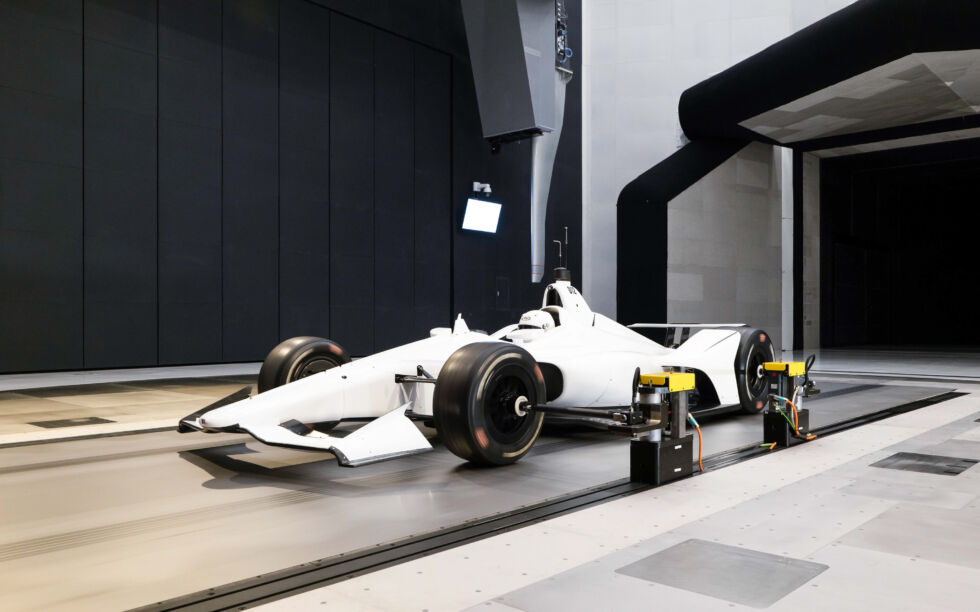
Honda
What happens next depends upon how the test room has been configured. For testing high-speed aerodynamic performance—for Acura’s forthcoming LMDh car, or the NSX sports car, perhaps—the test will probably involve the wide-belt rolling road. This 0.03-inch (0.8 mm) steel belt travels at the same speed as the air, with the car mounted on arms that hold it in place while allowing the wheels to rotate. The test also measures changes in lift, drag, and pitch.
The rolling road is not limited to testing a car head-on, either. It’s actually mounted on a 180-degree turntable that not only makes it easier for the engineers and technicians to set up their tests, but also allows them to study the effect of crosswinds and yaw.
Despite its impressive capabilities in this regard, such high-speed testing will probably represent a minority of the work performed at HALO. Road car aerodynamics are now becoming more important than ever as automakers electrify, since even small reductions in drag mean a boost in efficiency. For those kinds of tests, being able to reach 192 mph is of little use.
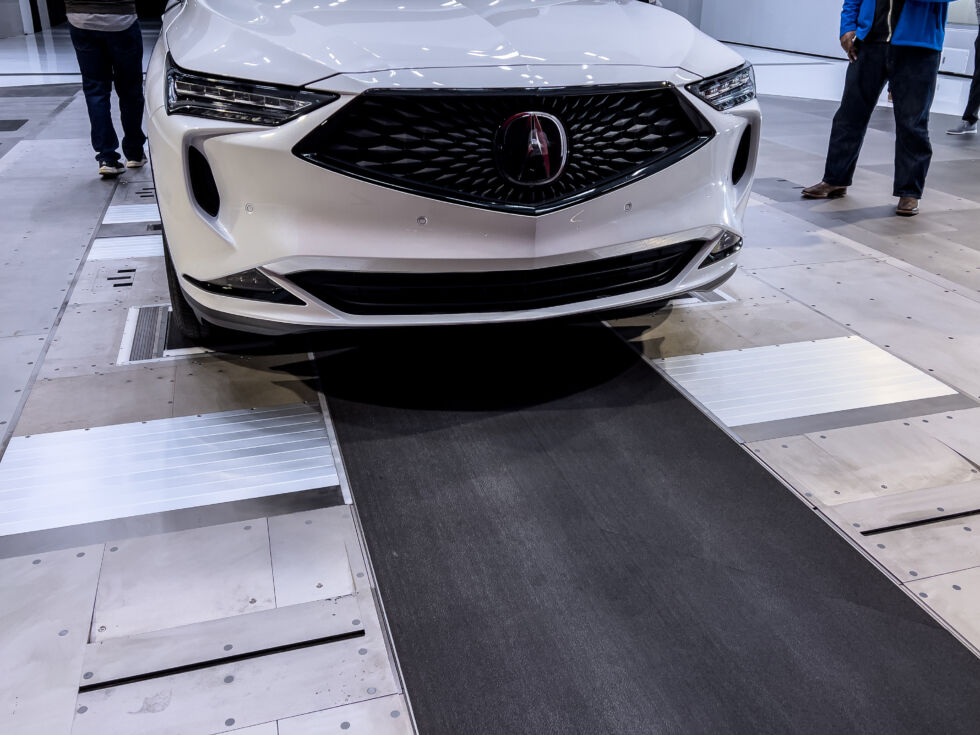
Jonathan Gitlin
This is why the tunnel was designed with swappable rolling roads. It takes about four hours to swap out one of the 44-ton (40 tonne) rolling road modules for the other. The second rolling road cam accommodate a maximum speed of 155 mph (250 km/h) and features five belts—one for each tire and a fifth that runs under the length of the vehicle inside the wheels’ track. Two slots appear in the floor ahead of each of the belts, controlling the boundary layer that would otherwise confuse the results.
The test vehicles have their brakes and suspension disconnected so the wheels can turn without parasitic drag (the cars are mounted on load cells which keep the vehicle at a constant ride height). Additionally, HALO has a laser scanning system to calculate a car’s frontal area in about two minutes—vitally important information if the results of the wind tunnel are to make sense.
Electrifying automakers aren’t just interested in streamlining their machines. Without the noisy symphony that is an internal combustion engine powertrain, everyone now has to up their game in terms of wind noise—also known as “aeroacoustics.”
-
For aeroacoustic testing the rolling road is covered, and arrays of microphones set up just outside of the boundary layer.
Jonathan Gitlin -
This is the wide belt rolling road module.
Jonathan Gitlin -
Engineers supervise an aeroacoustic test in the wind tunnel.
Jonathan Gitlin -
The microphone arrays can pinpoint noise from specific components or design features.
Jonathan Gitlin
The rolling road is not required for aeroacoustic testing, so the car sits atop an acoustic cover that protects the belt. (It’s presumably easier to just cover one of the two rolling road modules than create a third module for noise testing, since another module would take another four hours to swap out.) And instead of measuring aerodynamic loads, the test car is surrounded microphones—a total of 502 directional microphones arranged in acoustic arrays, with another 54 microphones placed inside the car. These microphones can tell engineers exactly which bit of the car needs a subtle tweak to quiet things down.
The acoustic arrays live just outside the wind shear layer, which is a remarkably calm place to be, registering a noise level of just 57dB even while the wind is blowing past just a few feet away. Honda was kind enough to let me clip into a harness and test this out myself—even at just 30 mph (50 km/h), you really feel the extra pressure of the air as you hold a long smoke wand into the stream to visualize the flow of air through a vent or across a hood.
To begin with, HALO will mostly concentrate on refining Honda and Acura’s North American offerings—the point of spending $124 million on a facility like this is because it saves time and money compared to paying for third-party tunnels here in the US, or shipping test models or cars to Japan. But HALO’s also been designed from the outset to accommodate others, whether that’s academic researchers, racing teams, or even other OEMs, with preparation bays hidden from prying eyes to maintain the kind of strict confidentiality that everyone in the industry expects.